Table of Contents
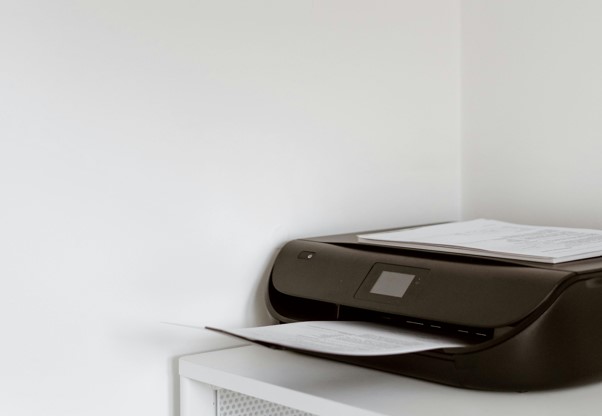
Introduction
A thermal printer is a printer that creates images by heating the coated thermal paper as it passes over the print head. They are commonly used in various applications due to their speed, reliability and low operating costs.
Types of Thermal Printers
- Direct Thermal Printers: These printers use heat-sensitive paper that turns black when heated. The print head selectively heats areas of the paper to create an image. Direct thermal printers are simple and do not require any ink, toner, or ribbon.
- Thermal Transfer Printers: These printers use a heated ribbon to transfer ink onto paper or other materials. The print head heats the ribbon, causing the ink to melt onto the printing surface. This type allows printing on a variety of media, including paper, plastic and fabric.
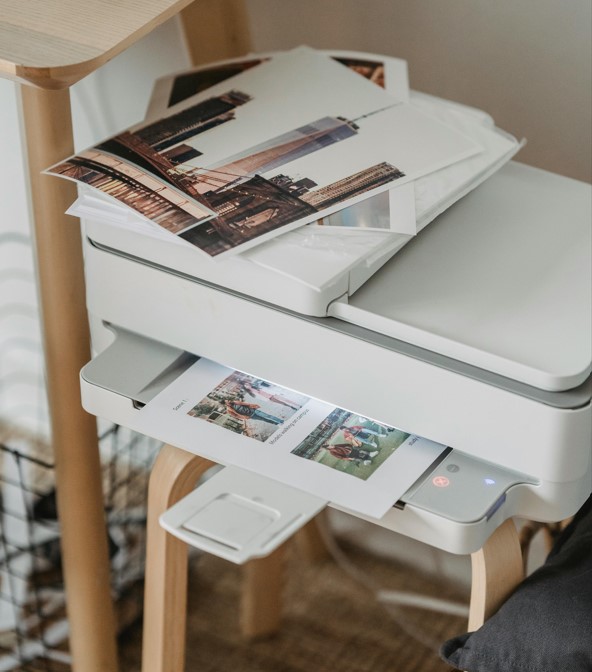
1. Direct Thermal Printing
Direct thermal printing is a straightforward and efficient printing process that relies on the use of heat- sensitive paper to produce images and text.
In this type of printing, the paper is coated with a chemical that changes color when exposed to heat. The thermal print head applies heat to the desired pattern, creating the image directly on the paper.
(1.1) Components of Direct Thermal Printer
- Thermal Paper:
- Specially coated with a mixture of dyes and developers that react to heat.
- The coating turns black (or any other color if specially prepared) when heated.
- Thermal Print Head:
- It consists of a series of small heating elements arranged in a row.
- Each heating element corresponds to a pixel in the image or text to be printed.
- Control Electronics:
- Manage timing and intensity of heating elements.
- Coordinate paper movement and ensure accurate printing.
(1.2) Steps in the Direct Thermal Printing Process
- Paper Feeding:
- Thermal paper is fed into the printer from a roll.
- The paper is passed through the printer across the thermal print head.
- Heating Elements Activation:
- The printer’s control electronics activate specific heating elements in the print head.
- The pattern of activation matches the desired text or image.
- Heat Application:
- Active heating elements generate heat in precise locations.
- Heat is transferred to the thermal paper as it passes beneath the print head.
- Chemical Reaction:
- Heat causes the colors and developers in the thermal paper coating to react.
- This reaction results in the formation of a visual image, which is usually black in color.
- The areas heated by the print head turn black, creating the printed output.
- Image Formation:
- As the paper continues to move, the entire process is repeated row by row.
- The resulting image or text is created directly onto thermal paper without the need for ink, toner or ribbon.
(1.3) Characteristics of Direct Thermal Prints
- Resolution:
- Thermal is determined by the density of the heating elements in the print head (measured in dots per inch or dpi).
- Common resolutions are 200 dpi, 300 dpi, and 600 dpi.
- Speed:
- Direct thermal printers can print fast, making them suitable for high-volume applications such as retail receipts and shipping labels.
- Durability:
- Prints are sensitive to environmental factors such as heat, light, and chemicals.
- Over time, exposure to these elements can cause the print to fade.
(1.4) Advantages of Direct Thermal Printing
- Simplicity: Fewer moving parts and no need for consumables such as ink or toner make maintenance easier and reduce operating costs.
- Reliability: Direct thermal printers are highly reliable for short-term applications due to their simple design.
(1.5) Limitations of Direct Thermal Printing
- Print Longevity:
- Printed images and text are not as durable as those produced by thermal transfer or other printing methods.
- Direct thermal prints are best suited for applications where longevity is not a primary concern.
- Environmental Sensitivity:
- Prints can be damaged by exposure to heat, light, and certain chemicals.
(1.6) Common Applications of Direct Thermal Printing
- Receipts: Widely used in retail for printing point-of-sale receipts.
- Shipping Labels: Common in logistics and shipping for printing labels and barcodes.
- Tickets: Used to print event or transportation tickets.
- Medical Records: Printing wristbands and labels for patient identification and specimen tracking in health care settings.
Direct thermal printing is valued for its efficiency and simplicity, making it a preferred choice for many everyday printing needs despite its limitations regarding print longevity.
2. Thermal Transfer Printing
Thermal transfer printing is a versatile and reliable printing process that uses heat to transfer ink from ribbon to a variety of media types.
In this type of printing, a ribbon coated with wax, resin, or a combination is placed between the print head and the paper. The print head heats the ribbon, transferring ink to the paper to create the image. This process is widely used to produce durable and high quality prints.
(2.1) Components of a Thermal Transfer Printer
- Thermal Transfer Ribbon:
- It consists of three layers: a base film, an ink layer, and a backcoat.
- When heated the ink layer melts and is transferred to the substrate.
- Print Head:
- It consists of a series of heating elements.
- Heats specific areas to transfer ink from the ribbon to the substrate.
- Substrate:
- The material on which the image or text is printed.
- May be paper, polyester, polypropylene, or other synthetic materials.
- Control Electronics:
- Manage the activation of heating elements.
- Coordinate the movement of the ribbon and substrate.
(2.2) Steps in the Thermal Transfer Printing Process
- Ribbon and Substrate Feeding:
- The ribbon and substrate are usually fed into the printer from a roll.
- They pass through the print head area together.
- Heating Elements Activation:
- The printer’s control electronics activate specific heating elements in the print head.
- The pattern of activation matches the desired text or image.
- Heat Application:
- Active heating elements generate heat in precise locations.
- This heat causes the ink on the ribbon to melt and transfer to the substrate.
- Ink Transfer:
- The melted ink solidifies upon contact with the substrate, creating a durable print.
- The ribbon moves along each line printed, exposing fresh ink for the next print line.
- Image Formation:
- The process is repeated line by line as the substrate and ribbon move.
- The resulting image or text is formed on the substrate with high precision and quality.
(2.3) Characteristics of Thermal Transfer Prints
- Durability:
- Thermal transfer prints are highly durable, resistant to stains, fading, and external factors such as heat and chemicals.
- Ideal for long lasting labels and tags.
- Quality:
- Capable of creating high-resolution images and text with clear edges.
- Common resolutions are 200 dpi, 300 dpi, and 600 dpi.
- Versatility:
- Can print on a variety of substrates including paper, synthetic materials and even fabrics.
(2.4) Types of Thermal Transfer Ribbons
- Wax Ribbons
- Wax-Resin Ribbons
- Resin Ribbons
(2.5) Advantages of Thermal Transfer Printing
- High Durability
- Produces long-lasting prints that withstand environmental stress.
- Suitable for labels that need to withstand harsh conditions such as external exposure or chemical contact.
- Versatility
- Capable of printing on a variety of materials, making it suitable for a variety of applications.
- High Quality
- Provides sharp, high-resolution prints with excellent readability.
(2.6) Limitations of Thermal Transfer Printing
- Cost
- Ribbon is required, which adds to operating costs.
- It is generally more expensive than direct thermal printing due to the consumables involved.
- Complexity
- More complex than direct thermal printing, requiring proper alignment and handling of ribbons and substrates.
(2.7) Common Applications of Thermal Transfer Printing
- Product Labeling:
- Used to label products with barcodes, serial numbers and other information.
- Industrial Labels:
- Ideal for creating labels that need to endure tough environments such as chemical drum labels.
- Asset Tags:
- Used to tag assets across industries to ensure durability and readability over time.
- Healthcare:
- Printing patient wristbands, prescription labels, and laboratory specimen labels.
Thermal transfer printing is valued for its ability to produce durable, high-quality prints on a variety of substrates, making it an essential technology in many industries that require reliable and long-lasting printed materials.